ATI’s Patented MagMap® (Magnetic Mapping) test is conducted by inserting an array of hall effect sensors in the core of the stator under test. The sensors are placed near the teeth of the core. While a DC current flows through a winding, the resultant magnetic field strength and polarity at each sensor is measured and used to map the magnetic field for that winding. The measured data is stored in the computer’s memory.
This process is repeated for each winding in the stator. The data is then analyzed by the computer to determine the correct number of poles, correct angular position and correct polarity for each pole as well as correct phasing from winding to winding. This Patented test is the most extensive test of coil placement, phasing, and lead connection conducted by any equipment available.
What began as a project to develop a better torque transducer/load test method soon developed into a rethinking of how torque is measured. As in all good research, the basic principles of physics were reexamined and, although all prior methods were studied, thinking was not allowed to simply begin where previous research had ended. The result was the invention of the digital torque measurement method now referred to as Digitorque®.
Digitorque®’s revolutionary method has all the advantages of load testing without its calibration / maintenance woes, typical slowness and high costs. Indeed, the Digitorque® method can measure hundreds of torque / speed points - enough to characterize the entire torque / speed curve including locked-rotor, pull-up, breakdown, and full load points - in just a few seconds. About the same amount of time most no-load and signature methods require. Simply put, this all-digital method renders laboratory results at no load speeds.
PATENTED Tests
MagMap ®
Digitorque ®

Our CLIENTS
Regal Beloit
GE Aviation
Whirlpool
Tesla
Harley Davidson
Honeywell
Baldor
Nidec
Franklin Electric
and many more...
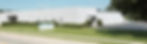
IN BUSINESS SINCE 1982
AUTOMATION
TECHNOLOGY
Our STORY
Automation Technology Inc. was founded in February 1982. During the first few years, ATI manufactured custom built test equipment primarily for the electric motor manufacturing industry. As a manufacturer of custom built equipment,
it quickly became clear the drawbacks associated with building custom equipment. Some of these drawbacks included long lead times, high costs
(and in turn, high prices), and difficulty with service and support.
​
It was evident that what the industry needed was a standardized test system packed full of "standard" features to accommodate nearly any testing requirement for a particular product category (i.e. stators, armatures, motors, rotors, etc.). With this goal, the people of ATI went to work developing "standardized" test systems. Today, with systems installed around the world,
ATI offers the industry's most advanced line of testing equipment.
MARKETS Served







